復合材料模壓使用2000噸油壓機更合適
復合材料的成型方法按基體材料不同各異。樹脂基復合材料的成型方法較多,有手糊成型、噴射成型、纖維纏繞成型、模壓成型、拉擠成型、RTM成型、熱壓罐成型、隔膜成型、遷移成型、反應注射成型、軟膜膨脹成型、沖壓成型等。金屬基復合材料成型方法分為固相成型法和液相成型法。前者是在低于基體熔點溫度下,通過施加壓力實現成型,包括擴散焊接、粉末冶金、熱軋、熱拔、熱等靜壓和爆炸焊接等。后者是將基體熔化后,充填到增強體材料中,包括傳統鑄造、真空吸鑄、真空反壓鑄造、擠壓鑄造及噴鑄等、陶瓷基復合材料的成型方法主要有固相燒結、化學氣相浸滲成型、化學氣相沉積成型等。
2000噸油壓機模壓成型(又稱壓制成型或壓縮成型)是先將粉狀,粒狀或纖維狀的塑料放入成型溫度下的模具型腔中,然后閉模加壓而使其成型并固化的作業。模壓成型可兼用于熱固性塑料,熱塑性塑料和橡膠材料。
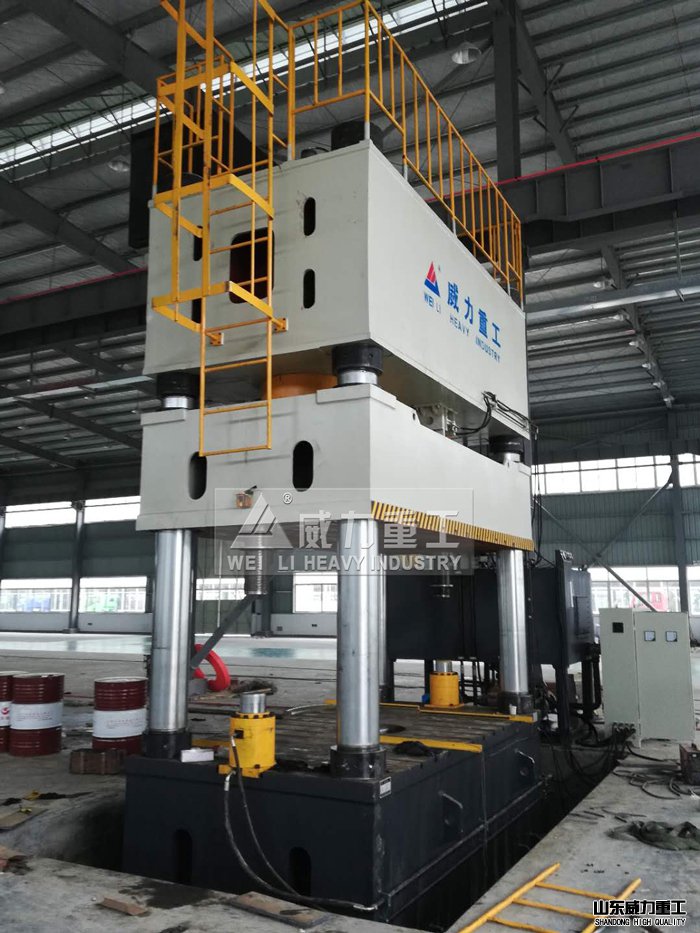
2000噸復合材料成型油壓機
2000噸油壓機加工復合材料優點:
(1)原料的損失小,不會造成過多的損失(通常為制品質量的2%~5%)。
(2)制品的內應力很低,且翹曲變形也很小,機械性能較穩定。
(3)模腔的磨損很小,模具的維護費用較低。
(4)成型設備的造價較低,其模具結構較簡單,制造費用通常比注塑模具或傳遞成型模具的低。
(5)可成型較大型平板狀制品,模壓所能成型的制品的尺寸僅由已有的模壓機的合模力與模板尺寸所決定。
(6)制品的收縮率小且重復性較好。
(7)可在一給定的模板上放置模腔數量較多的模具,生產率高。
(9)可以適應自動加料與自動取出制品。
(10)生產效率高,便于實現專業化和自動化生產。
(11)產品尺寸精度高,重復性好。
(12)表面光潔,無需二次修飾。
(13)能一次成型結構復雜的制品。
(14)批量生產,價格相對低廉。
模壓料的品種有很多,可以是預浸物料、預混物料,也可以是坯料。當前所用的模壓料品種主要有:預浸膠布、纖維預混料、BMC、DMC、HMC、SMC、XMC、TMC及ZMC等品種。
2000噸四柱油壓機加工復合材料
復合材料模壓工藝流程:
(1)加料:按照需要往模具內加入規定量的材料,而加料的多少直接影響著制品的密度與尺寸等。加料量多則制品毛邊厚,尺寸準確度差,難以脫模,并可能損壞模具;加料量少則制品不緊密,光澤性差,甚至造成缺料而產生廢品。
(2)閉模:加料完后即使陽模和陰模相閉合。合模時先用快速,待陰,陽模快接觸時改為慢速。先快后慢的操作方法有利于縮短非生產時間,防止模具擦傷,避免模槽中原料因合模過快而被空氣帶出,甚至使嵌件位移,成型桿遭到破壞。待模具閉合即可增大壓力對原料加熱加壓。
(3排氣:模壓熱固性塑料時,常有水分和低分子物放出,為了排除這些低分子物、揮發物及模內空氣等,在塑料模的模腔內塑料反應進行至適當時間后,可卸壓松模排氣一很短的時間。排氣操作能縮短固化時間和提高制品的物理機械性能,避免制品內部出現分層和氣泡;但排氣過早、遲早都不行,過早達不到排氣目的;過遲則因物料表面已固化氣體排不出。
(4)固化:熱固性塑料的固化是在2000噸油壓機模壓溫度下保持一段時間,使樹脂的縮聚反應達到要求的交聯程度,使制品具有所要求的物理機械性能為準。固化速率不高的塑料也可在制品能夠完整地脫模時固化就暫告結束,然后再用后處理來完成全部固化過程;以提高設備的利用率。模壓固化時間通常為保壓保溫時間,一般30秒至數分鐘不等,多數不超過30分鐘。過長或過短的固化時間對制品的性能都有影響。
(5)脫模:脫模通常是靠頂出桿來完成的。帶有成型桿或者某些嵌件的制品應先用專門工具將成型桿等寧脫,然后進行脫模。
(6)模具吹洗:脫模后,通常用壓縮空氣吹洗模腔和模具的模面,如果模具上的固著物較緊,還可用銅刀或銅刷清理,甚至需要用拋光劑刷等。
(7)后處理:為了進一步提高2000噸油壓機制品的質量,熱固性塑料制品脫模后也常在較高溫度下進行后處理。后處理能使塑料固化更加的完全;同時減少或消除制品的內應力,減少制品中的水分及揮發物等,有利于提高制品的電性能及強度。
本文由油壓機廠家整理,轉載請注明來自:www.tplijinxia.cn